Will Solar Supply Chains Pass the Circularity Test?
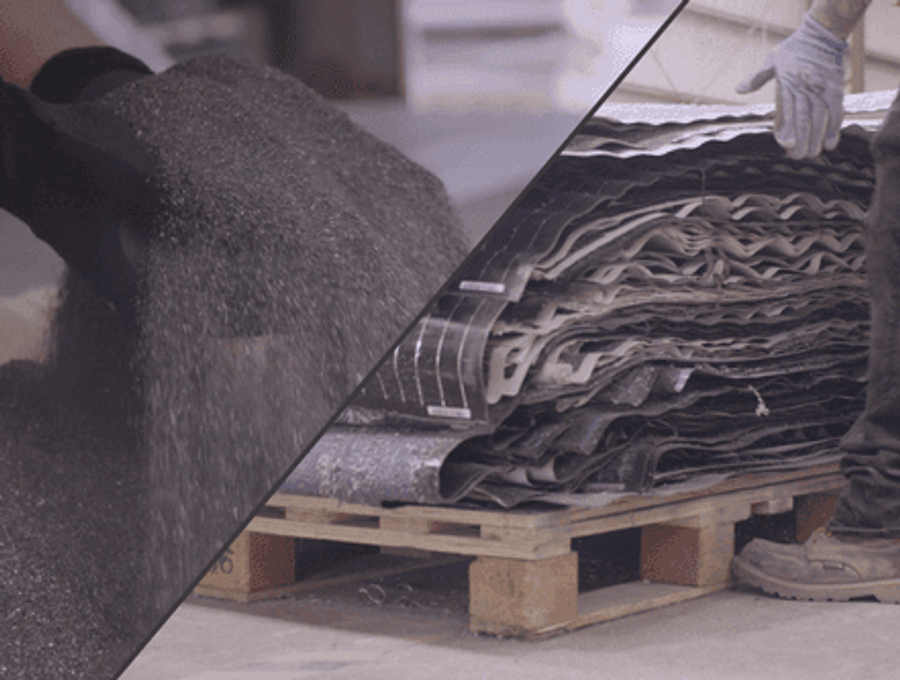
The solar industry eyes a circular future but faces pressure to recycle ageing panels, secure valuable materials and build greener global supply chains.
Solar power’s growth continues at pace, but with millions of panels installed every year, the industry faces a looming challenge—what happens when these panels reach the end of their life?
The solar supply chain is under pressure to become more circular, reducing waste and recapturing the valuable resources already embedded in photovoltaic (PV) technology.
According to SolarPower Europe, nearly 600 gigawatts (GW) of solar capacity was installed in 2024 alone, taking global installed capacity beyond 2 terawatts (TW). While that figure reflects growing momentum, it also signals an approaching waste problem.
With a lifespan of about 30 years, many of the panels installed today will be retired by 2050, putting material recovery and sustainable disposal under the spotlight.
The average global recycling rate for solar panels sits at just 14% according to the International Energy Agency (IEA) as of 2021. This means the majority of solar modules are still ending up in landfills, taking valuable metals and minerals with them—materials that could be returned to the manufacturing cycle.
“Achieving the global target of tripling renewable energy capacity by the end of the decade is possible with solar,” says Sonia Dunlop, CEO of the Global Solar Council.
“We need 1 TW of solar every year through 2030 and solar progress in more and more countries. That means action now to prepare for the future: smarter grids, faster permitting, bigger investments in emerging markets and serious workforce planning.”
Why panels leave the supply chain too early
Solar panels are built to withstand the elements, but even they degrade over time. Temperature swings, sunlight and general wear reduce efficiency. The US National Renewable Energy Laboratory estimates that panels lose around 0.8% of their output every year on average.
This means that after three decades, a solar panel might only operate at around 75% of its original capacity. As newer, more efficient models become available, up from 11% efficiency in 2000 to roughly 20% in 2025, replacing ageing panels becomes more economical than maintaining them.
However, that replacement cycle adds pressure on the back end of the supply chain. If the industry doesn’t scale up disposal and recycling methods, it risks creating tens of millions of tonnes of waste.
The IEA and the International Renewable Energy Agency (IRENA) estimate that by 2050, global solar waste could reach 78 million tonnes—around thirteen times the weight of the Great Pyramid of Giza.
Discarding panels means throwing away valuable and, in some cases, hazardous materials including silver, silicon, aluminium, copper and cadmium. While glass and aluminium are widely recycled, the infrastructure for recycling entire panels remains patchy and economically limited.
The IEA projects that only 22% to 49% of panels will be recycled by 2030 unless economic and regulatory conditions change. There’s real value to be had—materials recovered from these retired panels could be worth more than US$15bn.
New recycling models emerge
American manufacturer First Solar has been recycling panels since 2005 and claims to be the only solar company operating global, in-house PV recycling at industrial scale.
According to its 2024 Sustainability Report, it had 88,000 tonnes of annual nameplate recycling capacity by the end of 2023. First Solar also warns against relying on carbon-intensive production methods that undermine clean energy gains.
“If the solar manufacturing industry continues its business-as-usual approach by relying on cheap, subsidised coal electricity to produce polysilicon, it runs the risk of overtaking aluminium production in carbon intensity,” says Pat Buehler, Chief Product Officer at First Solar.
“We must act now to change course by actively reducing the carbon footprint of solar technologies while also investing in high-value recycling that addresses the end-of-life management of decommissioned solar panels in a sustainable manner. Our industry must embody sustainability, not simply pay lip service to it.”
California-based startup SOLARCYCLE is also developing infrastructure to keep valuable materials in use. It claims its proprietary recycling technology can recover over 95% of the silicon, silver, aluminium, copper and glass in end-of-life panels.
The company has worked with major players like CanadianSolar, EDP Renewables, Ørsted and AES, and is now piloting a “precycling” initiative with ENGIE North America to divert 48 million pounds of material from landfill.
“ENGIE’s precycling provision sets a new precedent for the utility-scale solar industry by proving that circular economy principles can be achieved without complex regulatory intervention and in a way that doesn’t require an up-front payment,” says Jesse Simons, Co-Founder and Chief Commercial Officer at SOLARCYCLE.
“We’re happy to work creatively with leaders like ENGIE to support their commitment to circularity, domestic energy and sustainability.”
The task now is to scale these initiatives to meet demand. With millions of new panels being deployed every year, integrating recycling into the solar supply chain is no longer optional—it’s a necessity.
To secure the materials that the industry itself depends on, and to avoid burying its waste in landfill, solar must build circularity into its global operations from the ground up.
Original Article – https://supplychaindigital.com/news/how-the-solar-energy-industry-can-build-circularity